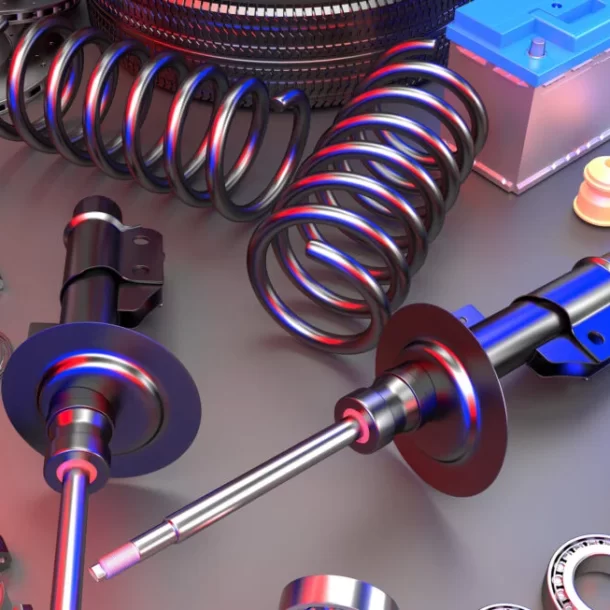
Automotive dismantling is a critical process in the automotive recycling industry, involving the safe and efficient removal of reusable components and materials from end-of-life vehicles (ELVs). Implementing best practices in automotive dismantling ensures safety, enhances efficiency, and maintains quality control throughout the process. In this blog, we will explore the key aspects of automotive dismantling, including ELV dismantling, catalytic converter recycling, EPR management, refurbished auto parts, and logistic solutions. Let’s delve into the world of automotive dismantling and uncover the best practices that drive this sustainable industry forward.
Efficient ELV dismantling begins with proper vehicle de-pollution, where hazardous fluids, such as fuel, oil, and coolant, are safely drained and disposed of. Next, trained professionals carefully remove and segregate various components, including engines, transmissions, doors, and electrical systems. Adopting standardized dismantling procedures ensures efficient disassembly, allowing for maximum salvage of reusable parts and materials.
Catalytic converters contain valuable precious metals that can be recycled. Implementing effective catalytic converter recycling practices involves proper identification, removal, and segregation of these devices during the dismantling process. Working closely with specialized recycling companies ensures the extraction of precious metals while adhering to environmental regulations and safety protocols.
EPR management places responsibility on automotive manufacturers for the safe and environmentally sound disposal and recycling of end-of-life vehicles. Effective EPR programs ensure that manufacturers comply with regulations, implement proper labeling and documentation, and establish take-back systems to facilitate the dismantling and recycling of ELVs. Collaborating with manufacturers and industry stakeholders helps maintain a seamless and responsible end-of-life vehicle management process.
Reusing refurbished auto parts not only reduces waste but also provides cost-effective solutions for vehicle repairs. Implementing quality control measures during dismantling and refurbishing ensures the availability of reliable and functional auto parts. Thorough inspections, testing, and proper documentation are essential in delivering high-quality refurbished parts to the market.
Efficient logistics solutions play a vital role in automotive dismantling. Streamlining transportation and storage processes reduces costs, minimizes environmental impact, and ensures timely delivery of dismantled components and materials. Effective inventory management systems and optimized supply chain strategies improve overall efficiency and customer satisfaction.
Adopting best practices in automotive dismantling is crucial for safety, efficiency, and quality control within the automotive recycling industry. By following efficient ELV dismantling procedures, embracing catalytic converter recycling, implementing effective EPR management, offering high-quality refurbished auto parts, and optimizing logistics solutions, stakeholders in this sector can contribute to a more sustainable future. As the demand for automotive recycling grows, upholding these best practices ensures the responsible management of end-of-life vehicles, reduces waste, and maximizes the reuse of valuable resources, driving the industry towards a greener and more sustainable path.
In the realm of automotive dismantling, maintaining stringent quality control measures is paramount. The process of dismantling end-of-life vehicles (ELVs) requires careful attention to detail to ensure the highest standards of safety, efficiency, and customer satisfaction. In this blog, we will delve into the essential quality control measures employed in automotive dismantling, including part grading, traceability, and customer satisfaction. Let’s explore how these measures contribute to a reliable and reputable dismantling process.
Part grading is a vital quality control measure that categorizes dismantled components based on their condition and functionality. Skilled technicians evaluate and assess the quality and usability of each part, classifying them into various grades (such as A, B, or C) based on their condition. This classification helps potential buyers make informed decisions about purchasing refurbished auto parts, ensuring that they receive parts that meet their specific requirements.
Traceability is crucial in automotive dismantling to ensure accountability and to provide customers with confidence in the origin and quality of the parts they purchase. Through robust tracking systems, each dismantled part can be traced back to its source vehicle, enabling accurate documentation and verification of the part’s history. This traceability enhances transparency, helps prevent counterfeiting, and provides customers with the assurance that they are receiving genuine and reliable components.
Customer satisfaction is at the core of quality control in automotive dismantling. Providing exceptional service and delivering high-quality parts are essential to building trust and loyalty among customers. This involves prompt and accurate order processing, thorough quality inspections, and effective communication throughout the sales process. Ensuring that customers receive the correct parts in excellent condition, along with responsive customer support, creates a positive experience and fosters long-term relationships.
Safety is a critical aspect of quality control in automotive dismantling. Adhering to safety regulations and best practices ensures that dismantling processes are conducted with the utmost care to protect both workers and customers. Implementing proper safety protocols, training employees, and providing them with appropriate personal protective equipment (PPE) are essential for maintaining a safe dismantling environment.
To enhance quality control in automotive dismantling, a commitment to continuous improvement is crucial. Regular evaluations, feedback from customers, and employee training help identify areas for improvement and implement necessary adjustments. By staying up-to-date with industry advancements, incorporating new technologies, and actively seeking innovative solutions, dismantling facilities can continuously enhance their processes and provide customers with the highest quality products and services.
Quality control measures in automotive dismantling are essential for maintaining safety, efficiency, and customer satisfaction. Through part grading, traceability, and a focus on customer needs, dismantlers can deliver reliable and high-quality components. Compliance with safety standards ensures a secure working environment, while continuous improvement drives innovation and excellence. By upholding these quality control measures, automotive dismantling facilities contribute to a sustainable industry, providing customers with the confidence and assurance that they are receiving top-notch products and services.
Ecoverva, a renowned name in the e-waste recycling industry, also stands as a trusted advocate for automotive dismantling. With a commitment to environmental sustainability and quality control, Ecoverva ensures that its automotive dismantling processes adhere to the highest standards. Through skilled technicians and rigorous quality inspections, Ecoverva guarantees that dismantled components are accurately graded, ensuring customers receive reliable and functional auto parts. Furthermore, Ecoverva prioritizes traceability, implementing robust tracking systems that enable the origin and history of each dismantled part to be easily traced. This commitment to transparency and accountability instills confidence in customers, knowing they are purchasing genuine and superior-quality components. With a focus on continuous improvement and compliance with safety standards, Ecoverva strives to provide an exceptional automotive dismantling experience, contributing to a sustainable and customer-centric industry.
We, Ecoverva is working tirelessly
in order to bring some peace in handling the E-waste in most proper manner.
-Read More
connect@ecoverva.com
Unit 1116, 1117 & 1119, 11nth Floor BPTP Park Centra, Sector 30 NH8, Gurgaon, Haryana 122001