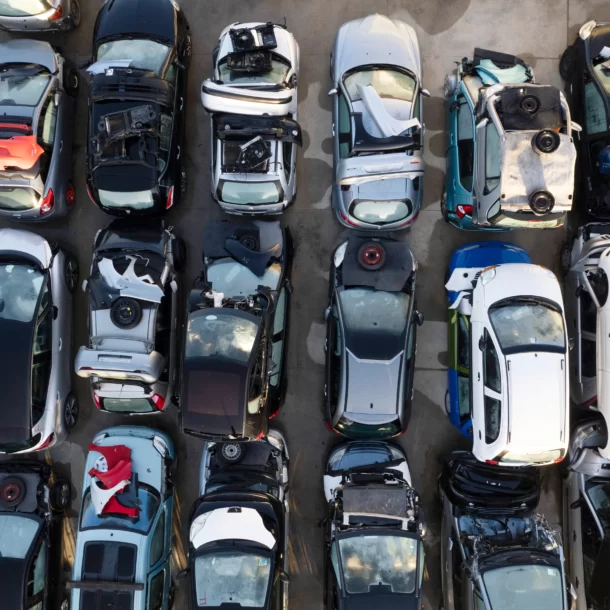
It is a complex process that involves the disassembly of vehicles and the recovery of valuable components and materials. To ensure the safety of workers, the efficiency of operations, and the quality of the output, it is important to follow best practices in automotive dismantling. Here are some key areas to focus on:
The importance of safety in auto dismantling: Safety is the top priority. A comprehensive risk assessment should be conducted to identify potential hazards, and workers should be provided with appropriate personal protective equipment (PPE) and training. Regular safety audits and inspections should also be conducted to ensure that safety protocols are being followed.
The key factors affecting the efficiency of automotive disposal: To maximize efficiency, it is important to have the right tools and equipment, a well-designed workflow, and a skilled and motivated team. Specialized tools such as hydraulic lifts, engine hoists, and power tools can speed up the disassembly process, while an optimized workflow can reduce the time and effort required to dismantle a vehicle. Effective teamwork is also essential to ensure smooth communication and collaboration between workers.
The Quality control measures in vehicle scrapping: Quality control is critical to ensure that recovered parts and materials meet the required standards. Part grading systems can be used to classify parts based on their condition and suitability for reuse. Traceability measures such as tagging and tracking can also help ensure that the right parts are being recovered and processed. Finally, customer satisfaction should be monitored through feedback surveys and other metrics.
The case studies and success stories of automotive dismantling businesses: There are many successful auto dismantling businesses that prioritize safety, efficiency, and quality control. These businesses often invest in training and certification programs for their workers, implement innovative technologies and processes, and build strong relationships with customers and suppliers. By following best practices, these businesses have been able to achieve high levels of profitability and sustainability.
The Importance of Safety in Automotive Disposal: Mitigating Risks with Proper Training and Equipment
It is an essential process in the automotive industry, allowing for the recycling and reuse of valuable materials and parts from end-of-life vehicles (ELVs). However, it is also a high-risk activity that poses potential dangers to the workers involved. As such, safety must be a top priority in vehicle dismantling operations. In this blog, we will discuss the importance of safety, including risk assessment, personal protective equipment (PPE), and training required in auto dismantling.
Before dismantling any vehicle, it is essential to conduct a thorough risk assessment. This includes identifying and assessing all potential hazards associated with the vehicle and the dismantling process. Hazards may include sharp edges, hazardous materials, and electrical components, among others. By conducting a risk assessment, dismantling teams can identify potential risks and implement appropriate measures to mitigate them.
Proper PPE is critical to protect workers from hazards during vehicle disassembly. PPE may include items such as safety glasses, gloves, steel-toed boots, hard hats, and respiratory protection. Each worker should be trained to use PPE correctly and consistently to ensure their safety.
Training is essential to ensure that all workers are aware of the hazards associated with automotive dismantling and are competent in the use of tools and equipment. Workers should receive training on the proper use of tools and equipment, such as hydraulic lifts and cutting tools, and safe work procedures. Regular training updates can help ensure that workers remain up-to-date on the latest safety procedures and regulations.
Automotive Recycling is a complex process that involves taking apart end-of-life vehicles (ELVs) to retrieve valuable parts and materials for reuse or recycling. As part of the process, it is essential to implement quality control measures to ensure that all parts are properly graded, traceable, and meet customer requirements. In this blog, we will discuss the quality control measures including part grading, traceability, and customer satisfaction.
Part grading is a crucial component of quality control in automotive dismantling. By assigning a grade to each part, dismantling operations can ensure that parts are accurately identified and meet customer requirements. Grades may be based on factors such as condition, mileage, and age of the part. Grading can help ensure that customers receive high-quality parts that meet their specifications and that dismantlers receive fair compensation for their efforts.
Traceability is another essential element of quality control in ELV dismantling. By implementing traceability measures, dismantling operations can track each part from the vehicle through the dismantling process to the final customer. Traceability may include recording the vehicle identification number (VIN), part number, and any other relevant information. Traceability can help ensure that parts are accurately identified and that customers receive the correct part for their needs.
Customer satisfaction is the ultimate goal of quality control measures and meeting customer requirements and expectations, dismantling operations can build a strong reputation and customer base. This may include offering warranties on parts, providing excellent customer service, and ensuring that parts are shipped on time and in good condition. Customer satisfaction can lead to repeat business and referrals, ultimately contributing to the success of the dismantling operation.
Quality control measures are essential in to ensure that parts are accurately graded, traceable, and meet customer requirements. By implementing these measures, dismantling operations can provide high-quality parts and materials for reuse or recycling and build a strong reputation in the industry.
Safety is a crucial element in automotive dismantling, and it is essential to take the necessary precautions to ensure that workers are protected from harm. By conducting risk assessments, providing proper PPE, and offering regular training, dismantling operations can mitigate potential hazards and create a safer work environment.
In conclusion, auto dismantling can be a highly profitable and sustainable business when best practices in safety, efficiency, and quality control are followed. By investing in the right tools, equipment, training, and processes, automotive dismantling businesses can ensure the safety of their workers, optimize their operations, and deliver high-quality products to their customers.
We, Ecoverva is working tirelessly
in order to bring some peace in handling the E-waste in most proper manner.
-Read More
connect@ecoverva.com
Unit 1116, 1117 & 1119, 11nth Floor BPTP Park Centra, Sector 30 NH8, Gurgaon, Haryana 122001